倉庫管理マニュアル作成の5つのポイントを紹介します。
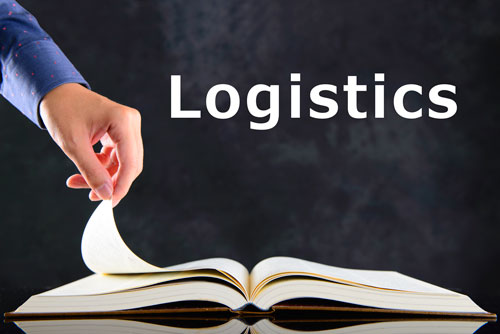
自社物流の誤出荷や在庫差異でお悩みではありませんか?本日は倉庫管理でまずは注目していただきたいポイントを8つ紹介いたします。
目次
5Sを徹底する
5Sをご存知ですか?5Sとは「整理」「整頓」「清潔」「清掃」「躾(しつけ)」のことを言いますが、倉庫現場では5Sに始まり、5Sに終わると言われるほど普及している改善活動であります。やはり作業環境が整っていないと誤出荷や在庫差異を発生させてしまう要因になります。倉庫が汚いと商品が棚からはみ出していても当たり前の風景になって何も気がづきませんが、倉庫が綺麗だと仮に一部の棚からみ商品がはみ出していてもすぐに気がつくことができます。つまりは商品の紛失を未然に防ぐことで結果的に在庫差異を減らすことができます。もし、汚れていて当たり前という社内意識があるのならそれはすぐに改善していくべきでしょう。綺麗な作業環境を作り出し、維持していくには5Sの中でも特に「躾(しつけ)」が重要です。人は誰でも注意されるとその時は気をつけようとしますが、それがなかなか持続しません。常に作業環境を整えるには粘り強く教えて習慣化していくしかありません。
入荷管理の徹底
誤出荷や在庫差異で悩む多くの企業が意外にも見落としがちな部分がこの入荷管理です。入荷管理は在庫管理の中でも1番最初の入り口です。例えば本来9ケース入庫するはずの商品を10ケースとしてシステムに入庫計上していたら、どんな問題が起きるでしょうか。入庫計上でミスをしていたら、後で在庫が合わないからといって倉庫の中を徹底的に探しても見つかるはずがありません。そのため、入庫担当者にケース数のチェックや入り数のチェックは徹底させる必要があります。誤出荷ゼロ、数量差異ゼロを目指す場合は、入荷時に間違いなく全量検品するべきでしょう。ただし、残念ながら企業様の中にはコストの関係から全量検品をしない、できない場合もあります。最終的にコストをとるのか、取引先やお客様との信頼をとるのか、その企業のビジネス形態や利益などを見ながら判断する必要がありそうです。
ロケーション管理
まだまだロケーション管理ができていない企業はたくさんあります。以前、弊社がコンサルティングした企業様もご相談いただいた当初はそのような状態でした。熟練のパートさんならすぐに商品を見つけ出すことはできても、新人の方ではなかなか時間がかかっているようで、効率的かと言われると残念ながらそうとは言い難い現状でした。倉庫内作業の原則として「考えさせない」という方針があります。それはなぜかというと自分で考えると誤出荷を引き起こす可能性があるからです。「この商品は確かあそこの棚の横にあったからそこからピッキングしよう。」と記憶を頼りにいわば思い込みで間違った商品をピッキングしてしまう恐れもあります。人の考えは人それぞれで環境によっても左右されます。そのため、倉庫現場における個人の判断は事故を誘発するリスク要因としてしっかりと認識する必要があります。解決策としては「考えなくてはいけない人」と「考える必要のない人」を明確に分けることです。前者の考えなくてはいけない人がマニュアルさえしっかり作ってしまえば、その他後者の考える必要のない人はみんな同じ手順で作業を行えるはずです。
確認作業の仕組み化
倉庫内作業でよく行われているのがダブルチェックです。しかし、実はこれもあまり効果的なものではありません。なぜなら一度チェックしたものを再度チェックするということは「一度チェックしているし大丈夫だろう」という心理が働き、二度目のチェックが甘くなってしまうからです。また、誤出荷がない日が続けば続くほど、「どうせミスなんて起こらないだろう」という心理が働き、段々とチェックが甘くなってしまう傾向にあります。このようにダブルチェックの精度は人の心理に大きく左右されます。しかし、作業者の注意力だけに頼っていてはいつまでたってもミスを減らすことはできません。ヒューマンエラーが起きた場合は、なぜ起きたのかを徹底的に解明する必要があります。もし、まだWMS(倉庫管理システム)を導入していない場合は導入するのが1番の近道かもしれません。納品書とピッキングした商品をスキャンすれば、間違いであればそこで気がつくはずです。ただし、その「納品書とピッキングした商品をスキャンする」ことは教育として徹底させることは必要です。
ただ、システムの導入は確かにミスを減らす可能性を見出してくれるものですが、それも完璧なものではありません。先ほど一例として出しましたが、「納品書とピッキングした商品をスキャンする」ことで確かにピッキングした商品が正しいかどうかの判断はできます。ただそれも100%ではありません。何故なら商品に貼られたバーコードが間違っているかもしれないからです。バーコード管理は確かに便利ではありますが、そのバーコードを商品に貼る作業でミスを犯していると、とんでもない結果になります。ただ、事前にその可能性もあることがわかっていれば、バーコード貼り付け時にいくつかの予防策を講じることはできます。
教育体制を整える
教育というとマニュアルを作って全体でミーティングすることを想像しがちですが、これが必ずしも正解とは言い切れません。何故ならミスをする人に限って複数人が参加するミーティングでの話はあまり聞いていないからです。結果としてミーティングを重ねることは、ミスの少ない人に繰り返しミスをしないように伝えているだけでその方たちの士気を下げている恐れがあります。そのため、誤出荷を減らそうと思うと、いつ、どこで、誰が、どんな作業内容に対してミスをしたのかを徹底的に分析していき、ミスをした要因が場所なのか時間なのか人なのか作業内容なのかを判断していく必要があります。もし仮に同じ人がミスを繰り返しているなら、一対一で教育することも忘れてはいけません。
まとめ
いかがでしたでしょうか?倉庫管理のマニュアル作成としては細かいものに目を向けると、ここには書き記せないほど多くのことがありますが、基本の部分はお伝えできたかと思います。トミーズコーポレーションでは自社物流にお悩みのお客様に物流コンサルティングサービスをご提供しております。誤出荷や在庫差異でお悩みの場合はまずはお気軽にご相談くださいませ。
トミーズコーポレーションの物流コンサルティングサービス
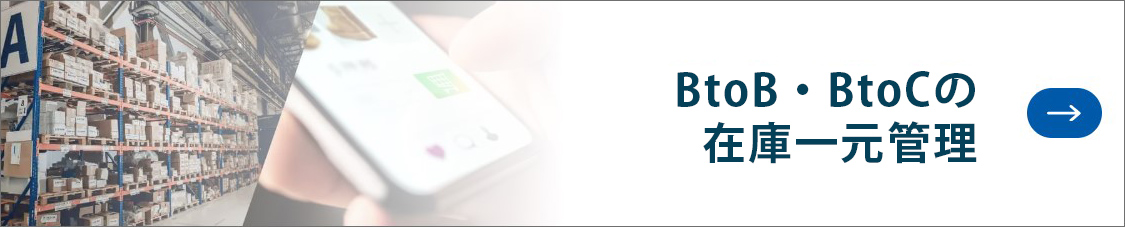