物流改善のヒントはピッキング効率の向上にアリ!
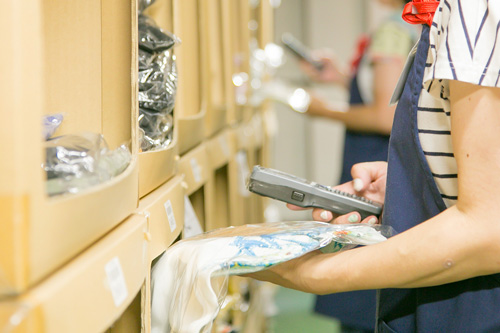
物流現場で作業スピードの課題に直面した際、最もよく聞かれるのが「無駄を省く」という言葉です。無駄を省くことは、単にコスト削減にとどまらず、作業効率の向上や全体的な品質改善にもつながります。しかし、無駄を省くためには、具体的にどの作業に焦点を当てるべきかを正確に把握することが重要です。
特に、物流現場での作業の中でも「ピッキング作業」は、その効率が作業全体のスピードに大きな影響を与えます。ピッキング作業の改善は、無駄な動作や時間を減らし、結果的にコスト削減と作業品質の向上を同時に実現するための重要なポイントです。今回は、物流現場におけるピッキング作業に注目し、その効率化や改善方法について詳しく解説していきます。最終的に、ピッキングの改善が全体の物流効率にどのように影響をもたらすかを見ていきましょう。
目次
ピッキングとは?
ピッキング作業とは、注文や出荷指示に基づき、必要な商品を倉庫内の指定された棚から適切な数量だけ取り出す作業のことを指します。物流業務において、ピッキングは非常に重要な役割を果たしており、その正確さとスピードが出荷全体の効率や納期遵守に大きく影響します。特に、ピッキング作業の効率化は、物流プロセス全体の無駄を減らし、コスト削減や作業品質の改善に直結します。
ピッキングの種類
ピッキング作業には、さまざまな種類がありますが、物流現場においては効率性やコスト、正確さを重視した適切なピッキング方式を選ぶことが重要です。主に、1つのオーダー(受注)ごとにピッキングを行う「シングル方式」、複数の出荷先分を1回の作業でまとめる「トータル方式」、そして仕分け作業を同時に行う「マルチ方式」という3つの主要なピッキング方式が存在します。それぞれの方式には独自の特長やメリットがあり、改善の余地も多くあります。以下で、それぞれのピッキング方式の特徴と改善ポイントについて詳しく解説します。
シングルオーダーピッキング
シングルオーダーピッキングとは、1つのオーダー(受注)単位で商品をピッキングする方式です。別名「摘み取り方式」とも呼ばれ、物流現場では一般的な手法です。この方式では、1つの注文に対して必要な商品だけをピッキングするため、注文間違いや商品の混入といったミスを最小限に抑えることが可能です。そのため、正確なピッキングが要求される場面では非常に有効です。
近年では、作業の正確さと効率をさらに向上させるため、ハンディターミナルを活用したピッキング作業が主流となっています。ハンディターミナルでは、事前に作成されたピッキングリストに基づき、バーコードをスキャンして検品作業を行うことで、作業の精度を向上させることができます。また、ピッキングミスを防ぎ、リアルタイムで在庫管理を行うことができるため、結果として作業効率と在庫管理の精度が大幅に改善されます。
シングルオーダーピッキングには、オーダーごとに商品をピッキングするため、特に同一商品の複数オーダーが発生した場合、作業者が何度も同じ棚に足を運ぶ必要があるという問題点があります。この「歩行距離の重複」は、作業者の負担増加や作業時間の無駄につながります。
この問題を改善するためには、動線の最適化や商品のロケーション配置の工夫が必要です。例えば、頻繁に出荷される商品を作業者のアクセスしやすい位置に配置したり、ピッキングカートのデザインを工夫して複数のオーダーを同時に処理できるようにすることが考えられます。
トータルピッキング
トータルピッキングとは、すべてのオーダー(受注)に対して必要な商品を最初に一括してピッキングし、その後、オーダーごとに商品を仕分ける方式です。「種まき方式」とも呼ばれ、複数のオーダーに対して同じ商品が含まれる場合に特に効率的な手法です。ピッキング作業自体を一度にまとめて行うため、同じ商品を何度も取りに行く必要がなく、作業の無駄を大幅に削減することができます。
トータルピッキングの大きな利点は、商品のピッキング時に歩行距離や無駄な移動を最小限に抑えることができる点です。基本的には、倉庫内に振り分けられたロケーションの順番通りに商品をピッキングしていくため、無駄な往復を避け、効率的に商品を集めることができます。一筆書きのような経路で作業が進むため、移動距離と時間を大幅に短縮することが可能です。
しかし、この方式には、ピッキングした商品を後でオーダー単位に仕分ける必要があるため、仕分け作業におけるミスや手間が増加するという課題も存在します。例えば、仕分けの際に誤って異なるオーダーの商品を混入させてしまうと、誤出荷のリスクが高まります。このような問題を解決するためには、仕分け作業の改善が重要となってきます。
仕分け作業の効率を向上させるためには、以下の改善策が考えられます。
仕分け専用のスペースやツールの導入
商品をピッキングした後に、効率的に仕分け作業を行うための専用スペースやツールを導入することで、作業ミスを減らすことができます。例えば、オーダーごとに色分けされたコンテナや仕分け専用のラックを用いることで、視覚的に商品を区別しやすくする方法が有効です。また、仕分けスペースの配置を見直し、作業者の動線を最適化することで、作業効率をさらに向上させることができます。
ピッキングと仕分けを統合したシステムの活用
ハンディターミナルや倉庫管理システム(WMS)を活用し、ピッキング作業中に自動で仕分けの指示が表示されるシステムを導入することで、作業精度を大幅に向上させることが可能です。例えば、バーコードスキャンを行いながら、どのオーダーの商品かをリアルタイムでシステムが判断し、その場で仕分けることができるようにすれば、後工程の手間が大幅に削減されます。このような自動化の技術は、作業のミスを防ぎつつ、効率的に改善するための有力な手段です。
作業者のトレーニングと教育
仕分け作業でのミスを減らすためには、作業者のスキル向上も欠かせません。定期的なトレーニングやマニュアルの見直し、または現場でのフィードバックを基にした改善提案を行うことで、ピッキングと仕分け作業の精度を向上させることが可能です。従業員の意識改革とともに、作業の質を高める取り組みが重要です。
マルチオーダーピッキング
マルチオーダーピッキングとは、複数のオーダー(受注)分を同時にピッキングしながら、並行して仕分け作業を行う方式です。物流現場では、オーダーの数が増えるほど効率的な作業が求められるため、この方式は非常に有効です。作業者は、ピッキングカートに複数のオーダー用のダンボール箱やオリコン(折りたたみコンテナ)を用意し、倉庫内のロケーション順に商品をピッキングしながら、それぞれのオーダーに対応する箱に商品を投入していきます。
この方式は、1回の移動で複数のオーダーを同時に処理できるため、作業効率が向上する大きなメリットがあります。特に、大規模な倉庫や多様な商品を扱う現場では、マルチオーダーピッキングの導入によって作業時間の短縮と無駄の削減が可能です。
マルチオーダーピッキングの最大の利点は、1度の歩行で複数のオーダーに対応できるため、歩行距離や作業時間を大幅に短縮できる点です。通常、シングルオーダーピッキングではオーダーごとに商品を取りに行く必要がありますが、マルチオーダーピッキングでは、同じ移動中に複数の注文品を同時に処理できるため、作業効率が飛躍的に向上します。
しかし、この方式にも課題があります。最も大きなリスクは、トータルピッキングと同じくピッキング中に商品を誤って別のオーダーの箱に入れてしまうことです。誤出荷のリスクを防ぐために、作業精度を高めるために以下の改善が必要です。
ピッキングカートの改善
マルチオーダーピッキングを行う際、ピッキングカートの設計は作業効率に大きく影響します。各オーダーごとの仕分けスペースが明確に区分されていないと、誤って別のオーダーの箱に商品を入れてしまうリスクが高まります。このため、カートには視覚的に区別しやすい仕切りや、オーダー番号が見やすく表示されているラベルを付けることが効果的です。また、仕分けスペースが広すぎると混乱の原因になるため、各オーダーに必要なスペースを適切に設計することが重要です。
デジタルアシストツールの導入
ハンディターミナルやピッキング支援システムを導入し、ピッキング作業をサポートすることで、ミスを防ぐことができます。たとえば、各オーダーごとの箱に正しい商品を入れるタイミングで、バーコードスキャンを行い、システムがリアルタイムで確認できる仕組みを整えれば、誤出荷のリスクを低減できます。また、音声ガイダンスやライトによる通知を使って、作業者が次にどのオーダーの箱に商品を入れるべきかを指示する「ピック・トゥ・ライト」システムも、誤操作の防止に有効です。
動線の最適化とレイアウト改善
マルチオーダーピッキングの効率をさらに向上させるためには、倉庫内のレイアウトや動線を見直すことが必要です。ピッキングルートが長くなりすぎると、カートに複数のオーダーを載せているメリットが相殺される場合があります。最適な動線を設計し、商品を効率的に集められるレイアウトを構築することで、作業の無駄を削減し、全体的な効率を向上させることができます。過去のオーダーデータを分析し、よく出荷される商品を取りやすい場所に配置することも重要です。
作業者のトレーニングと改善意識の向上
マルチオーダーピッキングの正確さを保つためには、作業者のトレーニングも欠かせません。特に、複数のオーダーを同時に扱うため、作業者が慎重かつ効率的に作業を進めるスキルを身につけることが求められます。定期的な教育やトレーニングを通じて、改善意識を高め、誤出荷を防ぐ取り組みを行うことが重要です。また、作業者からのフィードバックをもとに、現場での改善策を検討し、ピッキング作業全体を効率化するプロセスを継続的に進めることが必要です。
ピッキング作業効率を改善するためのツール
ピッキング作業の効率化を図るためには、適切なツールやテクノロジーの導入が欠かせません。近年、さまざまなデジタルツールや自動化技術が物流現場に導入されており、これらを活用することで、作業時間の短縮やミスの削減が可能です。以下に、ピッキング作業の効率を改善するために効果的なツールを紹介します。
ハンディターミナル(バーコードスキャナ)
ハンディターミナルは、ピッキング作業を支援するためのポータブルデバイスで、バーコードスキャン機能を備えています。ピッキングリストに基づき、商品を取り出す際にバーコードをスキャンし、ピッキングの正確性を確認することができます。
ハンディターミナルを導入することで、商品を手作業で確認する必要がなくなり、作業効率が大幅に向上します。また、リアルタイムで在庫状況を確認できるため、ピッキングミスの防止や出荷の迅速化にも役立ちます。特に、大量の商品を扱う現場では、作業者が商品を取り間違えるリスクが減少し、ピッキングの精度が向上します。
ピック・トゥ・ライト(Pick to Light)システム
ピック・トゥ・ライトシステムは、棚に取り付けられたライトやディスプレイを活用して、ピッキングする商品と数量を視覚的に作業者に知らせる仕組みです。作業者は、指定された棚のライトが点灯した場所から商品を取り出すことで、正確なピッキングを行います。
ピック・トゥ・ライトシステムを導入することで、ピッキング作業が直感的に行えるようになります。視覚的な指示に従って商品を取り出すため、作業者の熟練度にかかわらず、効率的かつ正確に作業を進められます。特に、作業スピードを重視する現場では、ピッキング指示をすぐに確認できるため、余計な確認作業が減り、全体の作業スピードが向上します。
ピッキングカートの最適化
ピッキングカートは、複数のオーダーを同時に処理する際に利用するツールで、効率的に商品を仕分けながら運搬できるように設計されています。カートには各オーダーごとのコンテナやダンボール箱をセットし、商品を適切に仕分けながら作業を進めます。
ピッキングカートの設計を工夫することで、作業者の負担を軽減し、誤出荷のリスクを低減することができます。例えば、各オーダーに対応する仕切りを明確に設けることで、商品を誤った場所に入れるミスを防止します。また、カートにはハンディターミナル用の台や作業効率を上げるためのアクセサリを設置し、作業者がスムーズに作業を進められるように工夫します。
倉庫管理システム(WMS:Warehouse Management System)
倉庫管理システム(WMS)は、在庫の管理やピッキング作業を一元的に管理するシステムです。オーダー情報に基づいてピッキングリストを自動的に生成し、作業者に指示を出します。また、商品のロケーションや出荷状況をリアルタイムで把握できるため、在庫管理とピッキング作業の効率を大幅に改善することが可能です。
WMSを導入することで、在庫情報やオーダー管理がデジタル化され、人的ミスを減らすことができます。さらに、過去のデータを活用してピッキング経路を最適化することで、作業者の移動距離を短縮し、効率的な作業を実現します。特に、大規模な倉庫では、在庫管理と出荷作業の連携をスムーズにするため、WMSの導入は欠かせません。
自動倉庫システム(AS/RS:Automated Storage and Retrieval System)
自動倉庫システム(AS/RS)は、商品を自動でピッキングし、保管や取り出しを行うシステムです。作業者が倉庫内を移動する必要がなく、オーダーに応じてシステムが商品を自動で出庫し、作業者に引き渡します。
AS/RSを導入することで、ピッキング作業を完全に自動化できるため、人手不足の解消や作業効率の大幅な向上が期待できます。また、作業者の移動が不要になるため、ミスやトラブルの発生率が大幅に減少します。特に、高頻度で出荷される商品や、保管スペースが広範囲にわたる倉庫においては、AS/RSは効果的です。
ピッキング作業の効率を向上させるための現場環境の改善
ピッキング作業の効率を最大限に引き出すためには、作業環境全体の改善が不可欠です。倉庫のレイアウト、作業者の動線、トレーニング、作業者の快適さに配慮することで、無駄を減らし、生産性を高めることができます。以下に、具体的な改善策を含めた提案をまとめます。
動線の最適化
ピッキング作業における効率化には、作業者の移動距離を短縮することが重要です。頻繁に使用する商品を出入口や主要動線に近い場所に配置し、商品のロケーションをゾーニングして一筆書きのように移動できる動線を確保することで、作業者の無駄な移動を大幅に削減します。これにより、作業者は必要な商品を最短ルートでピッキングでき、作業時間の短縮につながります。
作業エリアのレイアウト改善
作業エリアのレイアウトが不適切だと、作業者が無駄な動きをしがちです。作業者に合った棚の高さに調整し、適切な作業台を配置することで、作業効率を高めることができます。また、作業エリアの照明を強化し、視認性を向上させることで、ミスを減らし正確な作業を行えるようになります。このように、作業環境を整えることで、作業者が快適に作業でき、ピッキングミスも減少します。
作業者の教育とトレーニング
ピッキング作業の効率と正確さは、作業者のスキルに大きく依存します。ハンディターミナルやWMS(倉庫管理システム)の使い方を徹底的に指導し、効率的な作業手順を習得させることで、作業の精度と速度を向上させることができます。さらに、定期的な研修やフィードバックを通じて、現場の改善を継続的に進めることで、作業者のスキル向上と作業効率の持続的な改善が期待できます。
作業環境の快適化
ピッキング作業は、長時間の立ち仕事や歩行を伴うため、作業者の健康と快適さを考慮することが重要です。作業者の足元にクッション性の高いマットを敷いて疲労を軽減し、エアコンや換気設備を整えることで、快適な作業環境を提供することができます。これにより、作業者の疲労を軽減し、生産性の向上となります。
ピッキング作業の自動化による改善
ピッキング作業の効率を最大化するために、自動化技術の導入が進んでいます。自動化は、作業の正確さとスピードを向上させるだけでなく、人手不足やコスト削減にも対応する効果的な手段です。
自動倉庫システム(AS/RS)
自動倉庫システム(AS/RS)は、商品の保管から取り出しまでの全工程を完全に自動化する仕組みで、注文が入るとシステムが自動的に商品を取り出し、作業者へ届けます。これにより、ピッキング作業の効率が飛躍的に向上し、人的ミスが大幅に減少します。特に、大量の商品を扱う倉庫では、作業者の負担が軽減され、生産性が向上するだけでなく、自動化されたシステムは24時間稼働が可能なため、無駄な作業時間も削減できます。
ピッキングロボット
ピッキングロボットは、指定された商品を自動で取り出し、ピッキング作業を行う自動化技術です。ロボットは人間と異なり、24時間稼働できるため、効率が飛躍的に向上します。これにより、ピッキングミスが減少し、品質管理の向上に貢献します。また、ロボットの導入は人手不足の解消や人件費の削減にも寄与し、全体的な作業効率の向上と、現場の自動化を推進します。
自動搬送システム(AGV: Automated Guided Vehicles)
自動搬送システム(AGV)は、ピッキングエリアから出荷エリアまでの商品の運搬を自動化する技術で、作業者の移動を最小限に抑えます。AGVが自動で商品を運搬することで、作業者はピッキング作業に集中でき、物流フロー全体が効率化されます。これにより、作業スピードと精度が向上し、作業者の疲労が軽減されるだけでなく、全体的な生産性の向上にもつながります。
物流改善のための定期的な見直しと改善提案
物流現場では、常に変化する市場のニーズや新しい技術に対応するため、定期的な見直しと改善が重要です。現状のプロセスを評価し、改善提案を継続的に行うことで、業務効率と品質の向上が期待できます。
物流の見直しのポイント
現状のプロセス分析
定期的に物流フローを分析し、改善の余地があるかを確認します。ピッキング作業の時間、ミスの発生率、在庫管理の精度など、具体的な数値を基に評価することで、ボトルネックや無駄な作業を発見し、改善策を立案することが可能です。
KPI(重要業績評価指標)の設定とモニタリング
ピッキング作業の効率や正確さを測るために、KPI(重要業績評価指標)を設定し、定期的にモニタリングを行います。具体的には、「ピッキングミスの発生率」や「作業時間の短縮率」などの数値目標を設定し、その進捗を可視化することで、継続的な改善の指標とすることができます。
作業者からのフィードバック収集
作業者は現場の最前線で業務を行っているため、日常業務での問題や改善点に直接気づいています。そのため、定期的に作業者からフィードバックを収集し、改善に反映させることが重要です。これにより、実践的な改善提案が得られるだけでなく、作業者のモチベーション向上にもつながります。
定期的な改善提案の進め方
小さな改善の積み重ね
一度に大きな変更をするのではなく、小さな改善を積み重ねることで、無理なく効果的な改善が可能です。たとえば、ピッキングカートの配置見直しや、作業動線の微調整などがすぐに実行可能な改善となります。
テクノロジーの活用
物流現場には、最新技術を適用できる部分が多くあります。ハンディターミナルやWMS、ロボティクスの導入など、テクノロジーを活用することでさらなる効率化が期待できます。
PDCAサイクルの導入
計画(Plan)、実行(Do)、評価(Check)、改善(Act)のPDCAサイクルを取り入れ、継続的な改善活動を推進します。改善策の結果をしっかりと評価し、次のアクションにつなげることが重要です。
まとめ
いかがでしたでしょうか?
今回ご紹介したピッキング方式にはそれぞれ異なる特徴やメリットがあり、作業環境や業種によって最適な方法が異なります。シングルオーダーピッキングは、小ロットの正確な注文に向いており、ミスを減らす点で有効です。一方で、トータルピッキングやマルチオーダーピッキングは、大量出荷や複数のオーダーに対して、作業効率を高める手段として有効です。
ピッキング方式を選定する際には、取り扱う商品の特性、日々の出荷件数、作業者の動線やスキルなど、さまざまな要素を考慮することが大切です。また、近年では、ピッキング作業を支援するためのデジタルツールや自動化技術が進化しており、これらを活用することで、さらなる効率化とミスの削減が期待できます。自動化やデジタルツールを導入することで、ピッキング作業全体の精度とスピードを向上させることが可能です。
物流現場における改善は、一度の見直しで完結するものではありません。定期的に現場の状況を分析し、改善点を洗い出して最適化を図ることが重要です。物流環境は常に変化しており、取引先のニーズや市場状況に柔軟に対応するためには、継続的な改善が必要です。
トミーズコーポレーションでは、29年以上にわたりアパレル物流を中心に、さまざまな業種で効率的なピッキング作業を実現してきました。これまでの経験と実績を基に、お客様一人ひとりに最適なソリューションを提供することをお約束いたします。物流業務を外部に委託したいとお考えの企業様や、自社物流の効率化に課題を感じている企業様も、ぜひ一度ご相談ください。私たちは、物流全体の改善から、現場での具体的なピッキング効率の向上まで、幅広くサポートいたします。
物流の効率化は、単にコストを削減するだけでなく、作業者の負担軽減や顧客満足度の向上にもつながります。トミーズコーポレーションは、これまで培ってきたノウハウを基に、最適な物流運営をサポートし、お客様のビジネス成長に貢献します。ぜひ、最適な物流の実現に向けて、私たちと一緒に改善に取り組んでいきましょう。
ワンストップ物流サービス
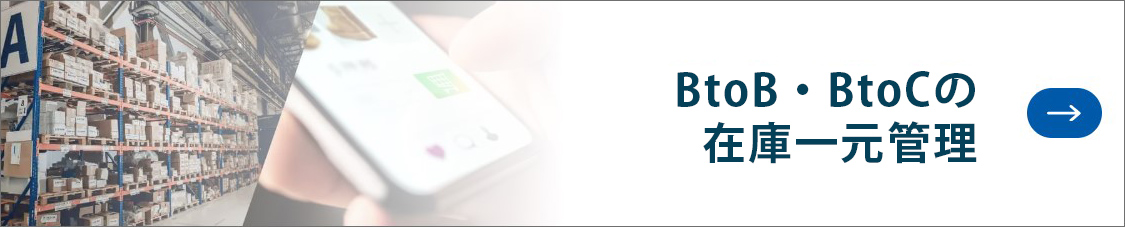